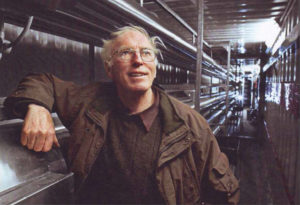
In the early 2000’s Solray Systems’ sister company (Solvent Rescue) undertook investigations into techniques for the safe destruction on organo-chlorine and other hazardous wastes. The destruction technique that provided the best results was based on using HydroThermal Liquefaction (HTL) to breakdown the waste at a molecular level and reform it within the reactor.
The by-products of these early experiments were:
- Harmless salts.
- Sterilized water.
- CO2
- A mixed hydrocarbon residue with characteristics very closely matching those of West Texas Intermediate crude oil.
- The remaining sludge comprises a typical mix of fertilisers including a high level of phosphate.
Solray refer to their patented HTL system as the DiagenTM Reactor as it mimics the geological process of Diagenesis – where biomass trapped underground is converted to crude oil over millions of years.
The Solray Diagen Reactor process is a continuous process with a conversion efficiency, of biomass to biofuel, of about 35% for average organic waste and 98% for plastic.
Solray Systems is focused on applying the DiagenTM process for producing Sustainable Biofuels meeting European Directive RED II (2016), for a Carbon Zero (Carbon Neutral) future.
Solvent Rescue also uses the same technology but is focused on hazardous waste destruction applications including organochlorine and PFOS wastes.
European Directive RED II (2016) specifies sustainable renewal fuels as those manufactured from biowastes such as sewerage sludge, pip/seed wastes from wine making, municipal wastes, forestry wastes (but not wood from long term permanent forests), algae (but not biomass taken from permanent wetlands) etc.
The DiagenTM biofuel closely matches the characteristics of West Texas Intermediate (WTI) crude with extremely low levels of oxygenates (unlike alcohol or Bio-diesel FAME – Fatty Acid Methyl Ester) and sulphur. This means it is an ideal “drop in” feedstock replacement for conventional oil refineries to displace fossil crude oils.
The refinery would continue to produce normal liquid hydrocarbon fuels, (Petrol, Diesel, Jet, etc) but as the feed stock meets RED II (2016) then the downstream products are also RED II 2016 compliant, i.e. Carbon Neutral Petrol, Diesel and Jet fuel etc.
Other products made from refined oil such as fertilisers, rubbers, plastics, pharmaceuticals and paints will also be made sustainably.
Solray Systems DiagenTM Reactor Technology allows the creation of a true circular economy with crude oil production at costs similar to, or below, average world crude oil prices.
The end product is pure hydrocarbon Bio-crude, not an ethanol or a biodiesel.
The first commercial DiagenTM plant built for biomass to biofuel conversion, was installed at the Christchurch Waste Water Treatment Plant to process algae grown in waste water. While algae employs the energy from sunlight to convert carbon dioxide into biomatter, it also needs other nutrients such as nitrogen, phosphate, sulfur and iron to manufacture essential proteins and DNA. The nutrients available in waste water provide an ideal source of these minerals for the algae.
The algae came from NIWA “state of the art” High Algae Growth Rate ponds fed by waste carbon dioxide from the DiagenTM process and was continuously harvested, without chemicals, by pumping a discharge stream through a simple static separator. When this algae has been grown and harvested correctly, then the remaining water is practically free of the nutrients and can be classed as essentially pure water. An additional benefit surplus nitrates are eliminated from the water.
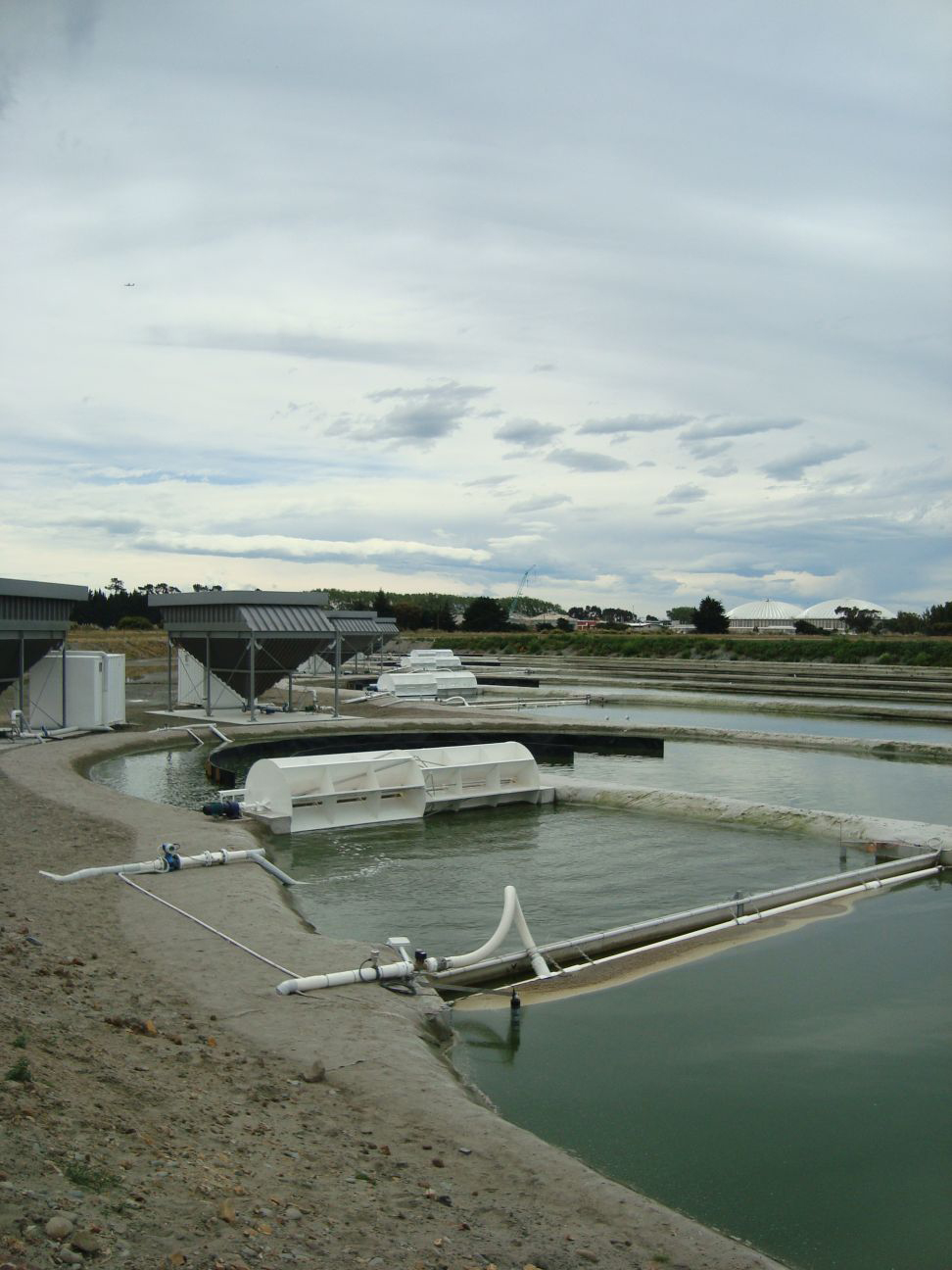
While many others working in this space are recovering oil from algae lipid, Solray is converting the whole algae biomass so it does not need culture specific species of algae. Algae can be grown in open air ponds or in bioreactors using photosynthesis and Carbon Dioxide and efficiency up to seven times greater than the best grassland production. Once harvested Solray can process the algae, along with any other biomass, to produce a renewable crude oil that is a genuine replacement for fossil petroleum.
The Christchurch City Council was extremely supportive in this project in making available space and use of the pond system. The Crown Research Institute NIWA was very interested in this project and has been of invaluable help by providing their advanced technology in growing algae in waste water as a source of algae.
At the time these were built they were the largest such ponds in the world.
Intensive farming, such as dairy and fattening enterprises, will benefit with a useful opportunity for alternative products. Effluent will be reduced or eliminated and the separated, purified water can be reused confidently.
This Algae project had to be curtailed when the area was hit by a powerful earthquake which badly damaged the algae pond system.